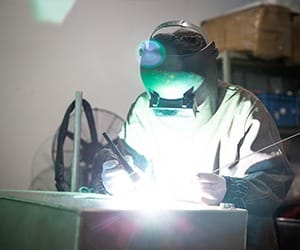

CNC technology advanced the field of precision machining, enabling manufacturers to produce sophisticated parts with exceptional repeatability. Utilizing Computer Numerical Control (CNC) machines, operators can program detailed instructions that guide cutting tools to remove material from a workpiece, achieving exquisitely accurate dimensions and surface finishes. The programmability of CNC machining offers several advantages over traditional methods, including increased productivity, reduced lead times, and improved part quality.
, Furthermore , CNC machines can handle a wide range of materials, from soft metals to durable alloys, allowing manufacturers to create parts for diverse applications.
In the modern manufacturing landscape, precision machining with CNC technology plays a crucial role in producing high-quality components for industries such as aerospace, automotive, and medical devices.
CNC Machining Processes for Efficiency
To truly amplify the efficiency of your CNC machining processes, a multi-faceted approach is crucial. Begin by meticulously analyzing your current workflow, identifying potential bottlenecks and areas for refinement. Implement precise toolpath planning software to minimize tool wear and material waste. Regularly fine-tune your CNC machine and ensure tooling is always in peak condition. Moreover, invest in operator training programs to improve skills CNC machining and promote best practices.
- Consider implementing a structured quality control process to identify and rectify any defects early on.
- Employ advanced machining techniques such as high-speed machining or multi-axis cutting for increased productivity.
By continuously assessing your processes and adopting innovative solutions, you can significantly optimize CNC machining operations and achieve greater efficiency.
Exploring Advanced CNC Milling Techniques
The realm of Computer Numerical Control (CNC) milling is constantly evolving, with innovative techniques pushing the boundaries of precision and complexity. From intricate prototypes to high-volume production runs, advanced CNC milling offers a versatile solution for diverse manufacturing needs. Mastering these techniques empowers manufacturers to achieve unparalleled levels of accuracy, surface finish, and material removal rates. Investigate the world of multi-axis machining, high-speed cutting, and advanced toolpath generation as we uncover the secrets behind creating complex geometries with remarkable efficiency.
- Designers are constantly seeking novel ways to optimize CNC milling processes.
- Implementing these advancements results in shorter lead times and reduced production costs.
- The prospects of CNC milling is bright, with ongoing research and development paving the way for even more remarkable capabilities.
Mastering CNC Programming Fundamentals
Stepping into the world of CNC programming can seem daunting. Jargon swims around, and complex concepts often confuse. But fear not! At its core, CNC programming is about delivering precise instructions to a machine. Think of it like writing a detailed recipe for the machine, dictating exactly how to cut, drill, or shape materials. By grasping fundamental concepts like G-codes and coordinate systems, you'll be able to design your own programs and bring your designs to life. This journey involves practice, but with patience and dedication, you can conquer the power of CNC programming.
Manufacturing's Next Chapter: CNC Automation and Robotics
The manufacturing/production/fabrication landscape is undergoing a profound transformation/shift/evolution driven by the increasing adoption/implementation/integration of CNC automation and robotics. These technologies are empowering/enabling/facilitating manufacturers to achieve unprecedented levels of precision/accuracy/detail, efficiency/productivity/output, and flexibility/adaptability/versatility.
- CNC/Computer Numerical Control
- Collaborative Robots
Furthermore/Additionally/Moreover, the integration/convergence/combination of CNC automation and robotics is unlocking/opening/revealing new possibilities for customization/personalization/tailoring in manufacturing. This allows businesses/companies/enterprises to produce/manufacture/create products/goods/items that are precisely/specifically/exactly tailored to the needs/requirements/demands of individual customers.
As a result/Consequently/Therefore, the future of manufacturing is bright, with CNC automation and robotics playing a pivotal role in driving/propelling/shaping industry growth/advancement/innovation.
CNC Machining Applications in Aerospace Engineering
The intensive requirements of the aerospace industry necessitate precision and accuracy in every component. Consequently, CNC machining has emerged as a crucial method for fabricating a wide range of parts used in aircraft, spacecraft, and related systems. From intricate engine components to lightweight structures, CNC machining permits the creation of high-performance parts that meet the stringent specifications of this field.
- Key applications of CNC machining in aerospace engineering include:
- Fabrication of turbine blades and engine components, requiring intricate shapes and tight tolerances.
- Fabrication of aircraft fuselages and structural elements, demanding precision and durability.
- Development of complex landing gear systems and other critical subsystems.
- CNC machining also plays a vital role in the production of aerospace tooling and fixtures, ensuring accurate assembly and testing.